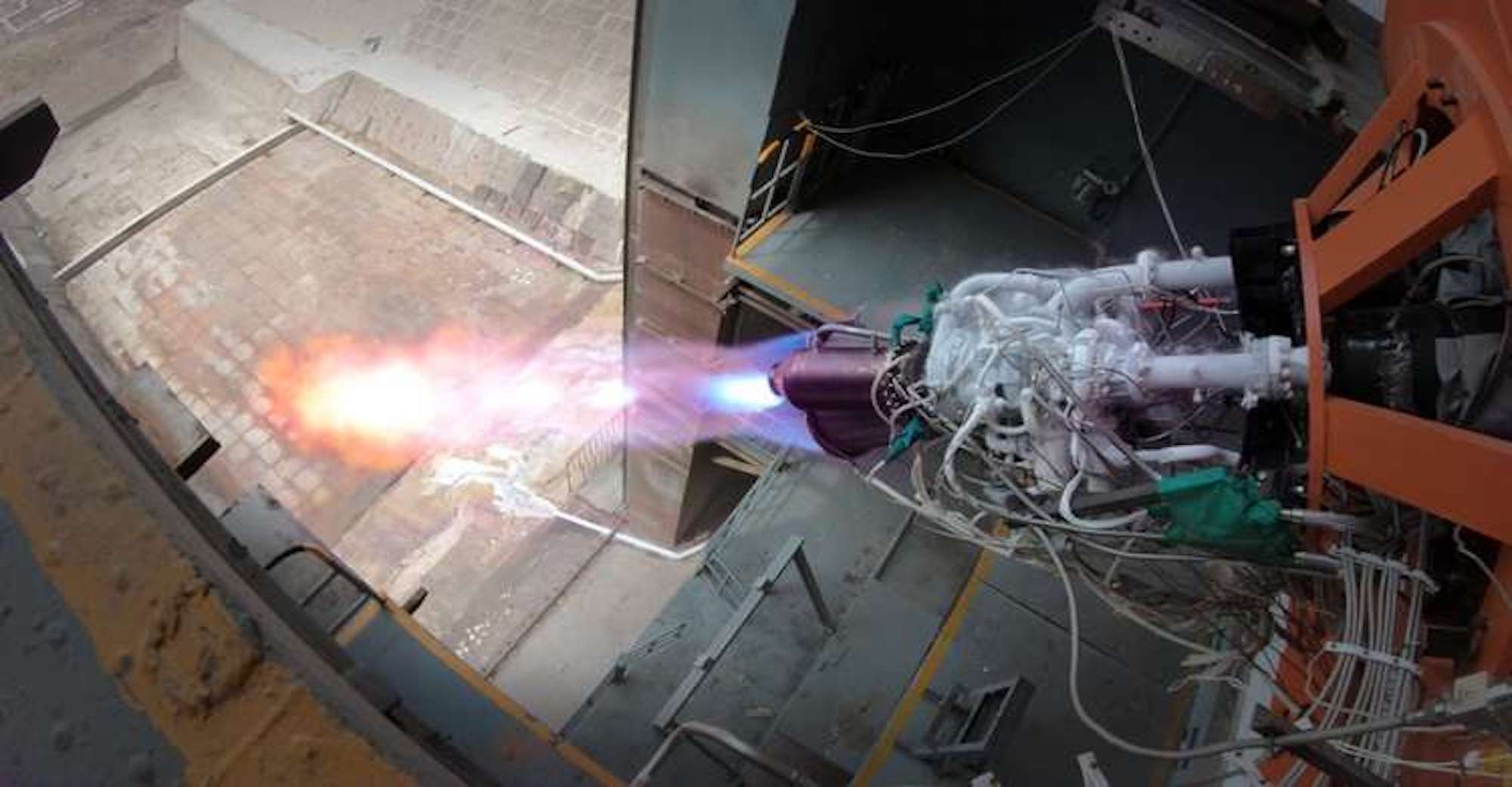
China's Reusable Liquid Rocket Engine, JD-1, Developed by iSpace, Passes 200-Second Continuous Variable Thrust Long-Range Test Run
Want to read in a language you're more familiar with? Please click the pink icon below for one-click AIPlease click the pink icon top right for one-click AI translation
JD-1, a reusable liquid oxygen-methane engine independently developed by Chinese aerospace manufacturer iSpace, successfully passed a 200-second continuous variable thrust long-range test run on July 8, 2020.
JD-1, a reusable liquid oxygen-methane engine independently developed by Chinese aerospace manufacturer iSpace, successfully passed a 200-second continuous variable thrust long-range test run on July 8, 2020.
This test verified the effectiveness of the JD-1 thrust regulation system solution and helped obtain accurate data on the engine’s continuous variable thrust function and performance. The test was a complete success. According to public information, it was the first time for China to complete a large-scale continuous thrust adjustment test for pump-fed cryogenic engines.
iSpace said that the test continuously varied thrust from high working conditions to low working conditions and then back to high working conditions (forming a V-shape), and the V-shape variation covered the actual flight condition requirements. To ensure the success of the continuous thrust adjustment test, a semi-physical simulation test of engine thrust adjustment and a simulated test run were carried out before the test. It was the first domestic simulation test of a liquid rocket engine thrust adjustable system, which has broken through the key simulation test technology of liquid rocket recycling.
It is understood that the engine’s continuous variable thrust capability is a necessary condition for the realization of vertical recovery technology of carrier rocket and is also one of the core technologies. On one hand, the variable thrust rocket engine can achieve optimal thrust control, thereby achieving precise control of the rocket return process; on the other hand, it can accurately control the overload of the carrier rocket during flight, ensure flight safety, and provide a good mechanical environment condition for the satellite.
iSpace technicians told reporters that compared with traditional stepped variable thrust, the engine thrust adjustment control system, used in JD-1’s continuous variable thrust test run, can drive the flow control valve to continuously adjust the flow of propellant, fulfilling the goals of continuous control of thrust and stable control of the thrust chamber mixture ratio under variable thrust conditions.
SEE ALSO: Chinese Private Aerospace Firm iSpace Completes 500-second Reusable Liquid Rocket Engine Test
To ensure JD-1’s continuous variable thrust ability, iSpace has made technical breakthroughs in engine thrust control law design, engine system fault diagnosis and reconfiguration control, engine control unit, flow adjustment mechanism, low-temperature continuous medium adjustment valve, semi-physical simulation test of engine thrust adjustment, simulated test run, and other aspects, which have been verified in this test run.
Developed by iSpace, Jd-1 is a 15-ton reusable liquid oxygen-methane engine. The engine adopts a multi-purpose design idea, including a basic type of fixed thrust, a variable thrust type and a vacuum type, three types in total. The latter two are derivates of the first type. The components of each type can be shared, which is conducive to reducing the R&D cycle and funding. It is understood that the 15-ton thrust engine can be used as the first-stage basic power of the launch vehicle in parallel with multiple same engines, or as a single engine of the vertical recovery power or the power of the upper stage of the rocket. It takes into account the needs of two stages. Not long before, JD-1 has completed several full-system, long-range test runs and a second start-up test run in succession, with a cumulative test run time exceeding 2,200 seconds. In the follow-up, JD-1 will continue to carry out ground tests, such as a swing test run, whole engine vibration mode test, various engine boundary tests, engine endurance and reliability test run, and other tests.
In the future, JD-1 series configuration engines will be used on hyperbolic II, a reusable launch vehicle independently developed by iSpace, with nine of them installed in the first stage and one installed in the second stage. The company plans to breakthrough and fully master the technology of reusable launch vehicles through a 100-km vertical take-off and landing test of the hyperbolic II substage. It will perform the first flight of the hyperbolic II launch vehicle in 2021. At that time, the company will grasp the reusable technology of the liquid propellant launch vehicle and fulfill another leap-forward improvement of China’s commercial aerospace capacity.